Overall Equipment Effectiveness (OEE)
Overall Equipment Effectiveness (OEE) is a standard used to measure
manufacturing productivity by identifying the percentages of manufacturing
time that is truly productive. An OEE score of 100% means only good parts
are produced (100% Quality), as fast as possible (100% Performance), with
no stop time (100% Availability).
To calculate the OEE value, the three underlying factors of Availability
(A), Performance (P) and Quality (Q) must first be calculated. The OEE
value
is then calculated as:

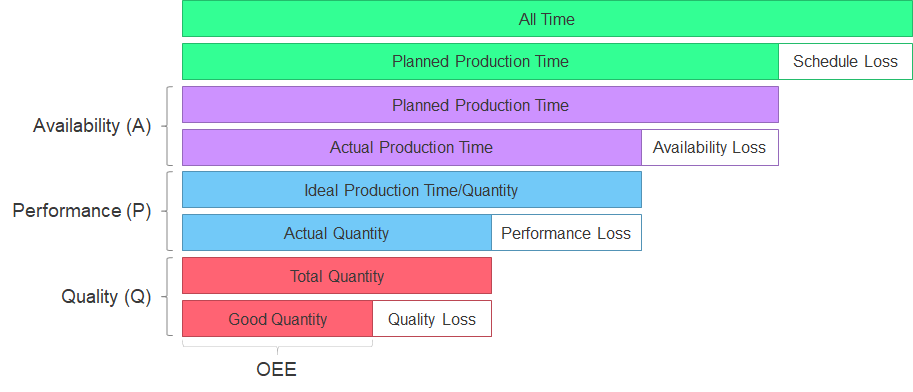
OEE Calculation
In IFS Cloud, OEE is calculated for work center resources over a period of
one workday according to the work center calendar. I.e., all time and
quantity transactions registered on a work center resource from shop order
and production schedule reports with the same
transaction date are considered in the OEE calculation.
Availability
Availability is the time the machine is planned for production but was
stopped with a downtime cause classified as availability loss, or was
reporting setup. The value is calculated as:

Planned Production Time is calculated as:

- Scheduled Working Time - The number of working hours for
the work center resource according to the work center calendar.
- Schedule Loss Downtime - Reported downtime for downtime
causes with OEE Factor = Schedule Loss.
Actual Production Time is calculated differently depending on
the option selected when the calculation was ordered:
Option A:

- Availability Loss Downtime - Reported downtime for downtime
causes with OEE Factor = Availability Loss.
- Setup Resource Hours - Reported machine setup time
considering the resource share.
Option B:

- Resource Hours - Reported machine runtime considering the
resource share.
- Performance Loss Downtime - Reported downtime for downtime
causes with OEE Factor = Performance Loss.
Performance
Performance represents the quantity the machine actually produced relative
what it ideally could have produced during the actual production time. This
can also be expressed as the time it ideally should have taken to produce
the actual quantity relative the time it actually took. The
value is calculated as:

Ideal Production Time is calculated as:
- Run Factor - The machine run factor from the shop order or
routing operation in hours per unit. The routing operation is used for
quantities reported for production schedules. If the factor unit is defined as
Hours for the operation, the value will not be multiplied with
the actual quantity. If the factor unit is Units/Hour,
the value is first converted to Hours/Unit. The run
factor will also be adjusted according to the defined Efficiency
for the work center resource. I.e., if the run factor is 1 unit/hour and
the resource efficiency is 80%, the run factor used in the calculation
is 0.8 units/h.
- Actual Quantity - The sum of the quantity reported as
completed and scrapped for the shop order operation or production
schedule.
Note: If you setup the run factor of the operation to reflect the
ideal cycle time, the Efficiency value defined for the
operation can be adjusted to a value
less than 100% to plan with a slower, more realistic cycle time.
Quality
Quality represents the ratio between good parts produced relative the total
quantity produced. The value is calculated as:
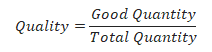
Good Quantity is calculated as:

- Total Quantity - The sum of the quantity reported as
completed and scrapped.
- Scrapped Quantity - The quantity reported as scrap.
Total Effective Equipment Performance
Total Effective Equipment Performance (TEEP) is a measure closely related to
OEE that measures the performance against total calendar hours whilst OEE
only considers the planned production time.
TEEP is calculated as:

Utilization is calculated as:

- All Time is 24 hours since the OEE and TEEP values are
always calculated per day.
Limitations
- The references shop order operation which a quantity transaction
reference must still exist (must not have been included in a mass
delete).
- The references production schedule receipt which a quantity
transaction reference must not have been moved to production schedule
reports history.
- A work center used to report production schedule must contain only
one valid resource on the transaction date. If the work center contains
several valid resources the time and quantity transactions are not
booked against any resource. Hence, the transactions will not be
considered in any OEE calculation.
- The performance calculation is using the routing/shop order
operation run factor. This may not represent the true ideal cycle time.
- Reworked quantities are not considered in the quality calculation.